Posting Rules | post new threads post replies post attachments edit your posts is are code is are are are | Similar Threads | Thread | Thread Starter | Forum | Replies | Last Post | | BrettB | Electrical: Batteries, Generators & Solar | 22 | 29-04-2019 00:30 | | Shanaly | Electrical: Batteries, Generators & Solar | 5 | 14-08-2012 05:15 | | sec906 | Health, Safety & Related Gear | 2 | 18-07-2010 17:43 | | teneicm | Navigation | 3 | 26-06-2010 14:05 | | bryan and wendy | Electrical: Batteries, Generators & Solar | 20 | 14-01-2010 08:42 | Privacy Guaranteed - your email is never shared with anyone, opt out any time.  - Forum Listing
- Marketplace
- Advanced Search
- All Topics Sailing
- General Sailing Discussions
- SailNet is a forum community dedicated to Sailing enthusiasts. Come join the discussion about sailing, modifications, classifieds, troubleshooting, repairs, reviews, maintenance, and more!
Ideas on securing wires inside mast?  If your halyards are external I read somewhere that wire ties along the bundle with the tails sticking out will keep the wires from slapping. That's the solution that Don Casey suggests, sounds like a simple solution. At copacabana: How do you hold the PVC against the wall of the mast for riveting? And why riveting, instead of some other method? ie screws Travlineasy, Your best option is a 3/4 inch PVC pipe conduit inside the mast, riveted to the inside of the mast wall. This way your wires won't interfere with your halyards and vice versa. I don't know why you think this will be expensive. I did mine last July when I hauled out. I bought PVC pipe at the hardware store and did the labour myself (2 or 3 hours). The hardest part is getting the pipe pressed against the mast wall to drill and rivet it in place. If your halyards are internal, there really is no other permanent solution that I'm aware of.  Once you get the PVC close enough to grab, the rivet will pull it tight against the mast. Putting a screw in will always be trying to push the PVC away until/if it 'grabs'. The 'wire straps left long' may even work with internal halyards, but best if the halyards are there first.. threading a new halyard or messenger through might be interesting... Either method requires pulling the cables and refeeding them - either into the conduit or with the wire ties attached.  The issue is, that the best solutions require taking the mast down. When I installed some extra accessories at the top of my Coronado's mast, I wrapped all the wires in closed-cell foam pipe insulation. This is not that nasty, black rubber foam that gets wet and disintigrates, this was a plastic-based foam that is extremely cheap at Home Despot, and very durable, and immune to humidity. I had the mast at home on saw-horses where I covered all the cables, pulled them up into the mast, and voila!- Silence. No drilling, no PVC conduit. First I removed some mast hardware to have a few free holes available. Then I used screwdrivers to push the pipe against the wall of the mast. It takes 2 people. One holds it and another drills and rivets. Start at one end of the mast and after the second fixing point the pipe stays pretty much in place, although you still need to push it firmly against the mast wall to rivet it. It's not exactly easy, but it's also not rocket science. It just takes patience. Riveting is the easiest and strongest method, but I suppose screws could work (or would they eventualy loosen in the pvc?). I suppose a good glue might also work (like 5200) if you roughened the PVC pipe with coarse sandpaper. The problem with Don Casey's method is that you haven't eliminated the greater problem of having wires (and now a bunch of wire ties) and halyards loose in the mast together. Eventually the rope chafes the wires or something gets tangled. I replaced all my mast wires when I put in the PVC conduit and all had a few big chafe points. The PVC pipe protects the wires and is a smooth surface that won't chafe your halyards. It's a cheap and easy upgrade.  I did the conduit with pop-rivets as told by knothead were you drill one small hole to hold the conduit in place with a bent coat hanger and then drill the second through the conduit and rivit it It worked really well and i was able to have a hole in the conduit at the combo steam/deck light were those wires exited the mast mid level If you’re gonna install a PVC conduit, I think securing it with an adhesive like 5200 is a far simpler way to go, and it saves the drilling of unnecessary holes in the mast… I did this about 15 years ago, mine’s held up fine… Simply assemble the conduit (I did one from the bottom, another from the top, to allow a break at the spreaders for spreader, steaming, and foredeck lights) and run a heavy bead of 5200 or similar along the conduit, then slide it in the mast (keeping the bead from making contact with the mast wall until you have it properly positioned, of course) Then, simply rotate the conduit to where you want it… Don't forget to run some sort of messenger line inside the conduit, especially if you're leaving a break somewhere, as I did... You'll be happy you did so when it comes time to run the wires, you can trust me on this (grin) Then, to insure you’ve got a consistent and adequate distribution of the sealant, slide an equivalent length of heavy, black iron pipe up inside the conduit to weigh it down, and ensure a good, solid connection with the mast wall… Let it sit until the adhesive cures, remove the black pipe, you’re done…  I've got the same problem. Jon's method above sounds good. I've got a long length of rebar that could be used in place of iron pipe. One thing I question is how do you satisfy the AYBC requirement of supporting the wire every 18 inches (to satisfy you would need a wire tie support every 18 inches coming down the mast, otherwise all of wires weight is supported from one point at the top). With wire in the mast seems nearly impossible. And how do you adequately support 40 feet or more of wire from the mast head? My wire just swing around and rub inside the mast, surprised they still work and have not broken loose from the top of the mast. "One thing I question is how do you satisfy the AYBC requirement of supporting the wire every 18 inches " I suppose that means doing what the utility companies do on powerlines. Run a separate steel cable, secure the other wires to it every 18". Oh did I forget? To mention do that while the mast is down, now insert the whole bundle in your conduit and secure it from the top, let the steel cable take all the weight. Sometimes there's no easy or practical way to retrofit. Know as a messager cable. Good idea. Maybe use a 1/16 inch AmSteel line instead of steel cable. No, a messenger cable is used strictly to move other wires from "this end" to "that end". It isn't used to secure them in place. A messenger cable needs to be at least twice as long as the wire run, so it can go back and forth, and still not be lost at either end. And available to move, without moving any existing wiring that remains in place. You previous description was for a messenger cable: Cable Construction Details The above definition is for a cable puller: Engineer's Corner -- Installing Communications Cable in Conduit: Pulling Lubricants, Blowing, Tension Calculations, Software, Fiber Optics, Friction Reduction  travlineasy said: (snip) I talked with a couple marinas and they recommended installing a PVC conduit in the mast, which would really be expensive. (snip) Has anyone else experienced this problem, and if so, I could sure use a solution. Thanks in advance, Gary Click to expand...  Just a thought for consideration- if you are ok with drilling some holes in the mast, maybe consider injecting some expanding foam insulation at various points to anchor the wires? Could easily be removed down the road if necessary. ??? Looks like my PO had done something similar. If foam is not exposed to UV should hold up just fine. Casey, Belden ought to know their stuff but I've always been taught, always heard the usage, of a "messenger line" (cable, etc.) as being the line you string between here and there, and use to pull other cables or wires back and forth. By riggers, electricians, anyone who has run one. And a "cable puller" from the electricians I know, is the thing (gizmo or single cable itself) you attach to one end of a cable, to pull it through. And then you need to run a new messenger line to run another new cable, because you've just pulled out the one that was there before. Does a "northerly" wind blow fom the north or the south? Despite all the definitions both ways, a northerly wind blows TOWARD not FROM the north. A North wind blows rom the north. A "northerly" one doesn't. Same same I suspect, just as so many people have taken to saying they will "insure" that something gets done, when they mean "ensure". Go back 20 years and the differences were clear, but today the meaning has been largely lost. Call me stubborn, adamant (two sides of the same coin) or simply wrong, but I'll stand by the only usage I've ever heard all these years and call Belden wrong on this one. Even if it is right in their internal industry jargon. I was looking at my mast last night. I have enough holes here and there to pull the wire out the side of the mast and attach a thick wire tie that is say 1 foot long. I would leave the tail on and that would restrict the movement of the wire some, and maybe enough to silence. Maybe you could try this. If you jam in the foam, what if you need to run wire in the future. Can they be removed? What about internal halyards? Gary, wait until you have to take down your mast at a future date and do it right with the PVC pipe then. It's something you can do yourself with one helper. It's not quite as complicated as you describe. In the mean time the foam blocks should do the trick, especially as you have all external halyards. Cheers! The last boat we installed a conduit in was a Pearson 33'. The mast was to be painted so we stripped the mast and installed the conduit. That took four hours. At 75.00 per hour, plus the conduit and rivets that came to about 300.60. Add in the crane fee, 150.00 each way, that comes to about 660.00 . We ended up doing a complete rerig, complete rewiring, added a led anchor light, spartite and a bunch of extra stuff so the final bill was more like 4 grand. FWIW.  You don't need pipe at all. Just take some zip ties and wrap them around your bundle of wires about every 3'. Leave the protruding ends of the zip ties on, and point them in different directions. You can even do this with the mast still on. Just pull all the wires out the top of the mast, and add the zip ties as you push the wire bundle down the mast again. Zip Ties. These will keep your wires from knocking against the inside of the mast. I've done this and it worked perfectly. You don't need pipe at all. Just take some zip ties and wrap them around your bundle of wires about every 3'. Leave the protruding ends of the zip ties on, and point them in different directions. You can even do this with the mast still on. Just pull all the wires out the top of the mast, and add the zip ties as you push the wire bundle down the mast again. Zip Ties. These will keep your wires from knocking against the inside of the mast. I've done this and it worked perfectly. Click to expand... Knothead, not quite. You can pull the whole wire bundle out the top, cut the zip ties and then drop a new bundle down again, if you ever need to add or change a wire. I've done this. Because the wires are still free inside the mast, I can't see much chance for chafing with a halyard. they will just move out of the way. I've used this method for 7 years and have not faced either of the problems you mentioned. Perhaps someone else has.  Why not put the wires in some PVC conduit and then wrap the zip-ties around the conduit to keep it from rattling? You would have to use more and/or heavier zip-ties because of the mass of the conduit. But, the wires would be protected from the halyards and you wouldn't have to drill holes in the mast. Might be awkward getting the conduit into the mast without dropping the rig to do it, however. Oh, and leave a messenger in the conduit for any future additions. EDIT: Oops. Never mind. I forgot about getting wires out of the conduit at intermediate places along the mast (spreader lights, steaming light, radar). Anytime a wire came out of the conduit, if the conduit wasn't firmly anchored to the inside wall of the mast, the wire would be subject to chafe. Gary, My mast is down and I'm going to do the same thing I did on last boat that I was very happy with. I have internal halyards too and slapping wires and halyards keep me awake. So I bought 50 feet of black poly spiral wrap from McMaster Carr and wrapped the cables in that making a nice neat bundle. Then I got so 2" thick Ethafoam polyethylene foam 2" thick. Its used for packaging things like LCD TVs and such on the corners. It is NOT styrofoam which is ridgid and breaks. I hold it against the end of the mast and trace around the mast with a marker, Then I use a sharp knife to cut out the oval to the outside dimension of the mast. I cut a small notch at the front edge for the wire bundle. I sharpen the edge on a sink tailpiece pipe to cut a round hole in the middle. The halyards all go up the center holes. I then use my whisker pole to push them in from both ends, spaced about 3 feet apart. Ahhh! Silent halyards! Life is good. Gary H. Lucas I got a dumpster full of that stuff. You can have it but we are 5,000 miles away from each other. One thing I question, the foam seems to be open cell. This would absorb water and stay wet for a long time. Could also get salt water for the blue water sailors. Once it gets salt in it, it will stay damp, and potential corrode your mast in the areas the foam is located.  My halyards are external (I made them that way during the refit). I went with expanding foam every two feet. Solid as a rock, and I can "yank" them out whenever/if the need arises. Worked out great (so far). I made sure not to fully fill the areas so water will drain down.. Top Contributors this Month 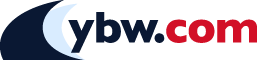 - Search forums
- Practical Boat Owner's Reader to Reader
External mast conduit- Thread starter webcraft
- Start date 1 May 2018
 Well-known member. I want to run an external conduit down the mast on Avy-J for cables. What material is best and how to attach it? _ W Assuming it's an aluminium mast with no space left inside, rather than a solid wooden one. I think it would have to be some kind of aluminium channel profile - plastic conduit is generally PVC and I'd expect it to go brittle after a few years and then crack when a halyard or sail whacks it. Both stainless and ordinary steel will be heavy and harder to work with; plain steel will rust and stainless will probably be quite expensive. Attach it with aluminium rivets (no need for great strength). Pete rogerthebodgerwebcraft said: . I want to run an external conduit down the mast on Avy-J for cables. What material is best and how to attach it? _ W Click to expand...  Was thinking of doing the same - would like to run a cable from tv aerial mounted on spreader down to deck. fredrussell said: Was thinking of doing the same - would like to run a cable from tv aerial mounted on spreader down to deck. Click to expand... At the moment the tricolor & Vhf cables are run externally in clips. I need to replace Vhf & fit steaming light. No access to inside of mast - would have to take the base off somehow. Also don't want cable slap in inside the mast. —W  Should the only option be for external conduit, then an alumin(i)um protective conduit seems the easiest way, secured by blind fasteners, As mentioned, PVC conduit will degrade under UV, and break off eventually. Such alumin(i)um will need its own coating of protection - possibly spray-on. Should the mast be hollow, then it is certainly possible to run the cables inside. Guidance on where and how to cut access holes, and 'make good', should be gained online from the likes of AllSpars or Selden, or even here. It's not a new requirement. Internal 'mast slap' may be prevented by fastening cheap cable ties tightly, at intervals, in a 3-star, configuration at short intervals around the cable bundle.  Will the mast not have a conduit for cables inside it? The Kemp mast for my 1980 Sadler 25 did. I wanted to fit a steaming light and ended up replacing the two core cable to the masthead with a tri, then ran a two core cable from there down to the new steaming light. The masthead cable up the conduit and the twin down inside the mast but outside the conduit. I obviously had to remove both the base and head bits...  PuffTheMagicDragonActive member. webcraft said: Also don't want cable slap in inside the mast. —W Click to expand... If it were me I'd go for a plan A of unstepping the mast and trying to run the cables internally. Obviously it won't be easy without a mouse down the cable conduit but you could get one of those cheap endoscope type cameras so you can see what you're doing internally. Maybe even fancier kit is available from tool hire shops. Once done it'll be a lot better job than external wiring conduits. It looks bad enough on old houses never mind a boat. . I don't think my mast has a cable conduit, nor do I think there is any easy way ot check. all indications are that cables have never been run inside this mast. But I will investigate further,l maybe post some photos. - W Are there any odd rivets visible on the mast that don't seem to be doing anything? It is just possible that a conduit, if present, might be attached that way. There's a thread from 2007 here: http://www.ybw.com/forums/showthread.php?116316-Wiring-a-Selden-mast&p=1197437#post1197437 It seems some masts have more than one conduit... What kind of boat/mast is it Webbie? A1Sailor said: Are there any odd rivets visible on the mast that don't seem to be doing anything? It is just possible that a conduit, if present, might be attached that way. There's a thread from 2007 here: http://www.ybw.com/forums/showthread.php?116316-Wiring-a-Selden-mast&p=1197437#post1197437 It seems some masts have more than one conduit... What kind of boat/mast is it Webbie? Click to expand... A1Sailor said: Are there any odd rivets visible on the mast that don't seem to be doing anything? It is just possible that a conduit, if present, might be attached that way. Click to expand... I would avoid using lots of rivets in the mast. It's May already, time to crack on with a quick fix. Dare I suggest running the cables up the back stay? Lots of dinghies have the luff rope track glued to the mast, as an alternative option. Plastic conduit will probably die of UV, even in Scotland, but it's not expensive to replace every few years, or when you drop the mast and sort an internal conduit. UV resistant plastic conduit is around, but it's usually black. A coat of white paint will help UV proof it anyway. Is it a luff-groove section, not a slider-track? I've seen cables glued in the corners of the luff groove when there's space.  I've experienced external conduit - plastic and aluminium and found it worthwhile to cable internally. The plastic was a UV disaster and the sight of a long section of alloy spearing into the sea with the resultant flapping of cables in the breeze convinced me the only way was up the inside. I guess all the halyards are external and you have no existing orifices to probe through - cables may be led through intenal ducts in the extrusion so counting rivets isn't always an option. I guess the mast is coming down anyway, so if the foot (or truck) can't be removed due to white powder syndrome, drilling a hole in the base will allow investigation - there should be one for drainage anyway.  If you must run a conduit externally, there's plenty of ally tube around such as here which can be fixed with saddles - https://www.metals4u.co.uk/aluminiu...-1voRNwEhKqcWC_i6bMLBcuD82mCX_CBoCY0kQAvD_BwE lpdsn said: If it were me I'd go for a plan A of unstepping the mast and trying to run the cables internally. Obviously it won't be easy without a mouse down the cable conduit but you could get one of those cheap endoscope type cameras so you can see what you're doing internally. Maybe even fancier kit is available from tool hire shops. Once done it'll be a lot better job than external wiring conduits. It looks bad enough on old houses never mind a boat. Click to expand...  You could add a layer of heatshrink tubing to reduce UV degradation. IME, mast cables don't last forever due to water ingress and corrosion anyway. You can buy UV rated co-ax and other cable. I would guess the lights are wired with 3 core, + for white, + for tricolour and -ve. But there are variations! Members online- Fr J Hackett
- AntarcticPilot
- snowbird30ds
- jamiepyoung
- Irish Rover
- Wandering Star
- James_Calvert
- Windy Andros
- EssexPrincess
- Sailing newbie selsey
- Guillemot592
- Baggywrinkle
- John_Silver
- lonederanger
Share this page - Forums New posts Unanswered threads Register Top Posts Email
- What's new New posts New Posts (legacy) Latest activity New media
- Media New media New comments
- Boat Info Downloads Weekly Quiz Topic FAQ 10000boatnames.com
- Classifieds Sell Your Boat Used Gear for Sale
- Parts General Marine Parts Hunter Beneteau Catalina MacGregor Oday
- Help Terms of Use Monday Mail Subscribe Monday Mail Unsubscribe
Electrical connections for the mast- Thread starter fred1diver
- Start date Jan 16, 2020
- Forums for All Owners
- Ask All Sailors
 Hey everyone, wondering how you all make the mast electrical connections? what do you think of a waterproof connection box? or do you prefer a wire thru hull? I’m leaning towards a waterproof box  justsomeguyfred1diver said: not sure if that is any good Click to expand Ok, good to know, thanks  Captain Larry-DHfred1diver said: yes that is what I was thinking of, but I also saw this model View attachment 174127 not sure if that is any good Click to expand Yeah I’m not familiar with those Not sure how you get the wires through the deck with that rgranger said: Not sure how you get the wires through the deck with that Click to expand  I have 3 water tight deck connections at the mast base (lights, wind vane, VHF). There is an access panel beneath the deck stepped mast and the cables are connected in one of the “water tight” junction boxes there. The VHF actually has its own through deck connecter. A drip loop in each of the wires above deck along with the through deck connecters keeps any water from running into the access area. I only take the mast down every couple of years, not as if I am a trailer sailer or have to take the mast down for winter storage. If I was a trailer sailer, I would definitely be looking for a more expedient way of disconnecting and reconnecting.  Assuming your mast is deck stepped you could consider this. Make a hole in the deck within the footprint of the mast step big enough to put a 1/4" or so PVC pipe. Be mindful of where this will be in the cabin. Epoxy a piece of the PVC pipe through the deck so that the pipe stands proud of the deck about an inch. That is to keep rainwater out. Thread your wires through the pipe and goop it up enough to prevent chafing. You probably want to have a junction box somewhere near the pipe inside the cabin. That will allow you to un-step the mast without cutting the wires. You'll want to be pretty certain that there isn't core rot where you want to put the hole. And you should probably remove 1/4' or so of core around the hole and fill with thickened epoxy a la Don Casey. I had through deck connectors on my Mark 25 and was wholly unsatisfied with them.  rgranger said: I assume you are talking about the electric wire that goes to the anchor/steaming light on the mast. If that is correct, I use one of these View attachment 174124 View attachment 174125 View attachment 174126 If that is what you are looking for, do a search for 12v marine watertight deck connection Click to expand  My C&C27 with deck stepped mast has 2 of the chrome plated glands shown on the right in post #2. One for the VHF antenna and one for the mast lights. The wire comes through the deck gland then to a connector - N-type for the VHF then a 4 pin water resistant plug for the mast lights. It ends up looking sort of like post #13 in the other thread but with a chrome plated feed through gland Deck to mast electrical connection  Serenity on HudsonI have the first connector in use for my solar panel which I take into the cabin while sailing and it sitting in the cockpit charging the battery while at dock. I also used one for my autopilot. After 5 years of plugging-unplugging the autopilot connection began to fail. I spread the prongs to get a better connection until the smaller one just broke off. Don't use the autopilot on my Capri 22 as it balances so well that I can leave the tiller for a couple of minutes without any significant course variation (as long as the wind is steady and not varying in amplitude or direction significantly). May add the autopilot this year so I can eat lunch while I sail without worry. Or use the facilities other than over the side. My last TP-10 would not calibrate on my Hunter 23.5. I burned out a TP-10 every two years on the Hunter because of excessive weather helm I just couldn't get rid of no matter how focused on sail trim. Water ballast just not a good choice for good sailing characteristics. Good for launch though.  Serenity on Hudson said: ... Don't use the autopilot on my Capri 22 as it balances so well that I can leave the tiller for a couple of minutes without any significant course variation (as long as the wind is steady and not varying in amplitude or direction significantly)... Click to expand SRWK 2015 - This site uses cookies to help personalise content, tailor your experience and to keep you logged in if you register. By continuing to use this site, you are consenting to our use of cookies. Accept Learn more…
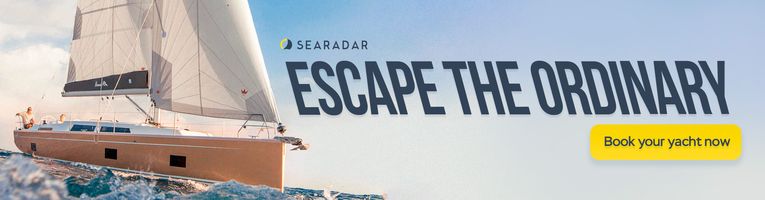 |
COMMENTS
Next, install the fixtures permanently using a sealant as an isolation barrier. Pull out any remaining slack at the butt of the mast. Trim all of your cables to a neat and even length. Leave enough slack for service lengths. Finally test all of the light fixtures through the mast and label the cables accordingly.
In this episode I show you step by step how I install conduit in sailboat masts.. *****DISCLAIMER Just because I showed you how to do it does not make you an...
You don't want conduit loose in the mast - particularly if you have internal halyards. You could pre drill the conduit.. mark the mast and drill the first hole and secure the conduit... the other holes should align with your marks. Assemble the conduit... tape to the outside of the mast. Drill the holes through the pvc conduit and though the mast.
270 posts · Joined 2006. #4 · Apr 1, 2014. would standard pipe insulation work instead of a plastic conduit, start at the bottom and slide the insulation up the mast and tape the insulation together at each of the butt ends with the wire inside. The insulation might lower or eliminate the noise of the wire hitting the mast.
Pop a new rivet into the conduit and move on to the next rivet. repeat the process until the conduit is secure again. Fill the off line holes with short aluminum rivets to complete the repair.u000bu000bIf you are very lucky the conduit will be loose at the bottom of the mast and still attached at the top.
Does anyone have a suggestion for securing a PVC conduit inside the mast for wires? If I rivet in place is there an easy way to hold the conduit in place while I drill the hole? Craig Tern #1519
Seminar: Basic Marine Electrical. Boating Tech Talk. Boating Tech Talk. Pacific Yacht Systems can design and install exactly what you need, so that you feel safe and enjoy your boat to its full potential. We offer design, installation, service, and support for marine electronics and electrical services.
Apr 1, 2014. #12. Many of you will find that your mast sections have a "T" or "C" shaped part of the extrusion that accepts a PVC conduit and holds it in place for the entire length of the conduit. Isomat, Sparcraft, Spartan, the MORC Sections from Dwyer, some Kenyon extrusions accept the conduit.
My mast has two slots which run full length beside the internal sail track. I ran 1" round PVC conduit from the mast base to 6" short of the masthead. It is held in place with a series of mast slides attached to the conduit every 12" by double cable ties attached at 45° angles. The conduit is bolted at the base through the mast track.
Depending on the size of the wires and the conduit to be used, these holes could be between 1/2 inch and 1 inch. If there is an internal conduit, install the wiring as detailed in Step 3. If there is no conduit, go to Step 2. Insert a PVC conduit into the mast through the hole at the top. Drill holes through the mast and conduit about every 4 ...
Images: 3. Re: Installing a Conduit in an Aluminum Mast. Use 1" or 1-1/4" PVC pipe riveted every couple feet or so along the forward face of the mast. Since it's not really load-bearing, you can use aluminum rivets. Make sure you cut the pipe in two near the location of your steaming and fore-deck lights so the wiring can exit easily.
Mark for the u-bolts and drill. Put the u-bolts over the conduit and into the holes. Glue the u-bolts to the conduit (your choice of glue). Roll the mast so the holes are now down. Pick up the whole mess and slide it inside the mast with the u-bolt legs toward the center.
Start about 1.5 inches away from the end of the fish and tightly spiral-wrap the electrical tape toward the end until youre about a half-inch past the wire end. Fold the excess tape down over the wire end and spiral the tape in the other direction. Now, bend each end of your newly wrapped wire about 10 degrees.
Not yet having my mast off I assume that the VHF and wind instrument cables travel thru a pvc conduit. Does anyone know if those cables are free or fastened? I would like to run my new wind instrument by going aloft and using the old cable to pull the new one down. Doug 1990 C30
A sailboat mast is like a long electrical fuse: one bad spot and the show is over. Critical failures are usually linked to standing rigging failures and can occur at toggle or tang attachment points, on the spar itself or at spreader tips and roots. Upper shroud tang fittings, near the masthead, need a close look.
Re: Electrical cable In mast. Drop a strong string down the mast with a small ring or some split shot fishing weights on it. From the base use a stiff wire with the end bent into a hook to fish the string out. From there you can pull your new cable and just abandon the old cable. 07-05-2019, 10:16.
Mast base electrical plug had some corrosion, but more disturbing was that all the wires reveal green corrosion after being stripped. It looks like the original wiring, 32 years old. I think I need to rewire the mast and also replace the panel to mast wiring. So questions arise. Does the mast wiring run in a conduit on a Newport 30 mast?
SBO Weather and Forecasting Forum Jim & John. If you have running rigging in the mast then thin walled PVC conduit would be recommended to keep electrical lines separate from wet halyards. Attach the conduit to the the inside of the mast away from the fairlead of the halyards and not in line with the sail tracks.
Some choices: 1) Feed the cables down through the mast step if possible. 2) Use a smaller diameter VHF connector, such as a TNC connector. 3) Use a bulkhead connector instead of a grommet for the VHF, see photo showing the mast cable for my previous boat with bulkhead connectors on both ends: Attached Thumbnails. __________________.
The last boat we installed a conduit in was a Pearson 33'. The mast was to be painted so we stripped the mast and installed the conduit. That took four hours. At 75.00 per hour, plus the conduit and rivets that came to about 300.60. Add in the crane fee, 150.00 each way, that comes to about 660.00.
The conduit appeared to be a very light wall 1/2" pipe. All but 2 of the pop rivers mounting the conduit had broken thru the conduit. I replaced it with PVC conduit, I think that it was 3/4" sch 40. I ran my wiring harness and antenna coax thru it. Those pop rivers protrude into the conduit and eat up some of the space, so bigger is better.
6,058. Visit site. Should the only option be for external conduit, then an alumin (i)um protective conduit seems the easiest way, secured by blind fasteners, As mentioned, PVC conduit will degrade under UV, and break off eventually. Such alumin (i)um will need its own coating of protection - possibly spray-on. Should the mast be hollow, then it ...
2,242. Beneteau 323 Manistee, MI. Jan 17, 2020. #9. I have 3 water tight deck connections at the mast base (lights, wind vane, VHF). There is an access panel beneath the deck stepped mast and the cables are connected in one of the "water tight" junction boxes there. The VHF actually has its own through deck connecter.